DoD Unveils Cybersecurity Maturity Model Certification
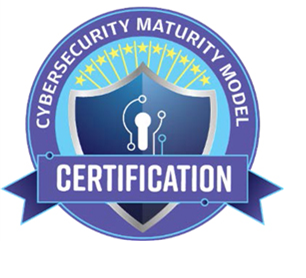
On January 30, 2020 the Office of the Under Secretary of Defense for Acquisition and Sustainment (OUSD(A&S)) released version 1.0 of the Cybersecurity Maturity Model Certification (CMMC). Version 1.02 was subsequently released on March 18, 2020. The CMMC is a unified standard containing five maturity processes and 171 cybersecurity best practices to standardize and ensure cybersecurity across the Defense Industrial Base (DIB), which includes over 300,000 companies providing goods and services to the United States Department of Defense (DoD). The framework has been designed to ensure that the DIB supply chain has adequate processes and practices in place to protect sensitive defense information.
What is the CMMC?
There are two main types of unclassified information the standard aims to protect:
- Federal Contract Information (FCI): FCI is information not intended for public release. It is provided by or generated for the Government under a contract to develop or deliver a product or service to the Government. FCI does not include information provided by the Government to the public.1
- Controlled Unclassified Information (CUI): Controlled Unclassified Information (CUI) is information that requires safeguarding or dissemination controls pursuant to and consistent with applicable law, regulations, and government-wide policies but is not classified under Executive Order 13526 or the Atomic Energy Act, as amended.2
The document, developed by cooperation between the DoD, Carnegie Mellon University and The Johns Hopkins University Applied Physics Laboratory, uses a framework to determine an organization’s cybersecurity maturity using third-party audits. Contractors still remain responsible for ensuring their organization is executing crucial cybersecurity best practices, but third-party assessments will now be required to ensure compliance with procedures and practices mandated by the basic safeguarding requirements set forth for FCI by FAR Clause 52.204-21 and for CUI as specified in NIST Special Publication 800-171 rev. 1’s 110 security requirements per DFARS Clause 252.204-7012.
According to Katie Arrington, Chief OUSD(A&S) Information Security Officer, “The CMMC is about level setting and making the industry get where they need to be to protect themselves and us. It’s about giving you the right resources to be able to provide that security, helping you to help us.”3 The CMMC will be used as an assessment tool to determine an organization’s cybersecurity maturity level for use as a requirement for a contract award.
What are the CMMC requirements?
In essence, the CMMC is a benchmark of best practices and processes against which an organization can measure its current cybersecurity infrastructure capabilities. There are five levels of certification consisting of processes and practices across 17 domains. In order for an organization to achieve a particular level of certification, it must have achieved compliance with the preceding lower level requirements. The CMMC provides a list of processes and practices for each domain for each level for a total of 171 practices at level 5.
Level 1:
An organization must perform 17 specified practices. “Basic Cyber Hygiene” is practiced for the protection of FCI according to the requirements specified in 48 CFR 52.204-21 “Basic Safeguarding of Covered Contractor Information Systems”. No maturity processes are assessed at this level as the organization performs the practices but does not necessarily have documentation in place. Examples of level 1 practices include (but are not limited to): limiting data access to authorized users; limiting the use of portable storage drives; authorizing, permitting and controlling remote access; enforcing the use of passwords; destruction of media containing FCI; and monitoring of information systems against malicious code. Many organizations that have already been awarded DoD contracts will likely already have most level 1 requirements in place and most DoD contracts are anticipated to require level 1 certification.
Level 2:
In addition to level 1 practices, an organization must perform an additional 55 specified practices. Level 2 requires documented practices and policies and includes some of NIST SP 800-171 rev 2 requirements. “Intermediate Cyber Hygiene” is practiced to protect CUI. Practices cover the following domains: Access Control, Awareness and Training, Audit and Accountability, Configuration Management, Identification and Authentication, Incident Response, Maintenance, Media Protection, Physical Protection, Personnel Security, Risk Assessment, Security Assessment, System and Communications Protection, and System and Information Integrity.
Level 3:
In addition to level 1 and 2 practices, an organization must perform an additional 58 specified practices. “Good Cyber Hygiene” practices ensure the security of CUI, including all NIST SP 800-171 rev 2 security requirements.
Level 4:
In addition to level 1, 2, and 3 practices, an organization must perform an additional 26 specified practices. At this level, organizations must be proactive in measuring, detecting and defending advanced persistent threats, including audits of historical data. Organizations have systems in place to review and measure effectiveness and can take corrective actions if threatened by a threat’s changing tactics. This level is most likely the minimum level expected of prime government contractors.
Level 5:
In addition to level 1, 2, 3, and 4 practices, an organization must perform an additional 15 specified practices and have standardized and optimized procedures across their entire organization. Enhanced and sophisticated cybercapabilities are optimized to detect and respond to cybersecurity threats.
How do I know if my organization needs to be CMMC certified?
All DoD contractors, including subcontractors will need to achieve CMMC certification to be awarded DoD contracts as long as your company does not solely produce COTS products. This includes government prime contractors and their subcontractors, although the DoD has not stated what level of compliance must be achieved and maintained. Meaning, subcontractors and smaller organizations may not need to achieve level 5 compliance. If your organization does not handle CUI but handles FCI, your organization will need a minimum of Level 1 CMC certification. It is anticipated that the DoD will specify the required CMMC level in requests for information and requests for proposals.
How can my organization become certified?
Organizations are not permitted to provide self-certification. Certification will be handled by the CMMC Accreditation Body (www.cmmcab.org), a not-for-profit independent organization. The CMMC AB will establish a CMMC Marketplace which will include a list of approved certified third-party assessor organizations that companies can contact to schedule assessments. No set pricing structure has been determined and CMMC certification will be valid for a period of 3 years. The OUSD(A&S) has estimated that certification to level 1 should be no higher than $3,000 and that grants will be made available to assist small businesses.4
What should my organization do now?
Organizations in the DoD chain of supply should familiarize themselves with the CMMC requirements and evaluate their current practices and procedures and identify gaps as certification will soon be a requirement for contract awards. While some organizations may already be able to achieve compliance, others may need to consider contracting with outsourced IT companies and, if doing so, should also verify that organization’s CMMC compliance. A thorough assessment and gap analysis can help determine your organization’s desired level of maturity and guidelines toward compliance. Depending on your desired level of maturity, implementation of cybersecurity monitoring and development of a system security plan will need to be developed and implemented as part of your organization’s routine processes. Katie Arrington has stated that CMMC requirements could be included in DoD solicitations as early as November 2020.5 However, she has stated that CMMC certification will not be required until the time of contract award, allowing contractors additional time to obtain certification.
For more information, the Office of the Under Secretary of Defense for Acquisition & Sustainment has created an FAQ page at
https://www.acq.osd.mil/cmmc/faq.html.
Download the CMMC at:
https://www.erai.com/customuploads/newsletter/CMMC_ModelMain_V1.02_20200318.pdf
1https://www.acq.osd.mil/cmmc/docs/CMMC-V0.6b-20191107.pdf
2https://www.archives.gov/cui/about
3https://spycloud.com/the-latest-from-dods-katie-arrington-on-cmmc-and-next-steps-for-dib-suppliers-awaiting-cmmc-audits/
4https://spycloud.com/the-latest-from-dods-katie-arrington-on-cmmc-and-next-steps-for-dib-suppliers-awaiting-cmmc-audits/
5https://www.govconwire.com/2020/05/katie-arrington-cmmc-requirements-in-rfps-expected-in-november/